
Modern Higo MKV
Machining form and function, but at what cost?
Project overview
The objective of this project is to create a lighter and stronger knife while exploring how to make tool holdings in a CNC. Aluminum, being the ubiquitous material that it is, makes it the perfect choice for exploring its art form and creating this piece.
Many are hesitant to make this due to the complexity of the machining process, but why don’t I give it a go?
Pocket Knives
Some people treat it as purely a tool and others collect them for their artistic form. I wanted to make something that can be both. Something that can evoke the feeling of weightlessness while still looking durable enough to put through the paces in the field.
The Experts
Throughout my time designing this knife, I also went to talk to some experts on knife making. One such place being Evan, the owner STRATA in Portland, Maine. He gave me much needed advice to make a better knife. One of the things he told me was that knives that have a belly, commonly found on western style knives, are not super useful in day-to-day situations as the belly is useful for rocking when cutting food stuff. Therefore, it makes more sense to go for a more box cutter like shape commonly referred to as a Reverse Tanto or Wharncliffe. They tend to have an edge that is mostly flat. Commonly found on Japanese Designs for pocketknives such as the Higo no Kami. Such a blade shape is also similar to a utility blade knife offered by the big tool brands such as Milwaukee or Dewalt.
The Higo no Kami is commonly used in Japan by students in school to sharpen their pencils and do various day to day tasks. A single beveled blade, although tends to wander when cutting straight down, is better for wildling away materials that are harder or shaving things. Such a design will also allow the blade to be hardened more for better edge retention, staying sharp for longer.
Research
There are truly a lot of options to choose from in this space. The price ranging from affordable to astronomical and designs radical to utilitarian. From building a mood board, I learned that there are many different tastes but a distinct lack of skeletonized designs. This is most likely associated with the astronomical machining times needed to pocket out each facet.
When interviewing potential users, it was found that most people preferred a flipper design that had a liner lock. They selected this due to the low-profile nature of a knife with those features along with the ease of maintenance. Although automatic/spring assisted knives are also popular among users, they are not legal in every state to carry day to day, therefore was not considered an option.
The User
The target users of this product are those who are interested in outdoors activities such as camping, fishing, or overlanding. Pocketknives in this space is generally used for the purposes of widdling branches for starting fires or cutting packaging open for a meal. While the overall weight of a product is not necessary always the top priority for everyone, it still holds some weight in everyone’s mind to make sure things are light enough to not be a burden.
Alex, who is in the image to the right, is a fan of driving overland and camping in very remote locations to get the best camping experience. He prefers to purchase artesian equipment over name brand ones as he feels they are more personalized to his likings.
Materials
D2 (Aristocrat) Tool Steel as chosen for the blade and all other high wear parts such as the spacers and the lock bar due to its inherent properties as a tool steel. It also has a high chromium content allowing for the blade to be more stainless than most knife steels. This chromium content also makes it a challenge to machine with a machinability score of 24/100 (Aluminum being 90/100).
Aluminum and Brass was chosen for the handle due to its ease of machining. Aluminum is very corrosion resistant and light, while brass gives off an exotic feel while calling back to the original inspiration behind the design (Brass Higo no Kami).
Phosphors Bronze washers are used to make the blade action as smooth as possible with it’s self lubricating properties.
Version 1
Version 1
It was decided that the CNC would be the only viable option to achieve my vision of making a knife that would be skeletonized with what I have access to. Therefore, I set out to make something for an existing platform that allowed me to practice the intricacies of machining out of aluminum and the challenge of getting all the tolerances just right. So, I went out and got the CIVIVI Elementem to study how they designed their knife and the processes they used.
3D Printing a test fit model
CNC milling the first version of the scales
The two sides ready to be faced off
Test fit
Version 2
Version 2
Milling this was surprisingly much faster than version one as I upgraded my tools and optimized my files. Although each milling step took over 3 hours, I was able to use the same amount of time to create twice the amount of product. However, tolerance issues started to manifest which needed to be addressed in order to achieve the quality feeling of using one of these blades. Another problem was the fact that I tried to make the profile so thin that it actually managed to bend in the soft jaws leading to a thicker iteration that is not as ideal.
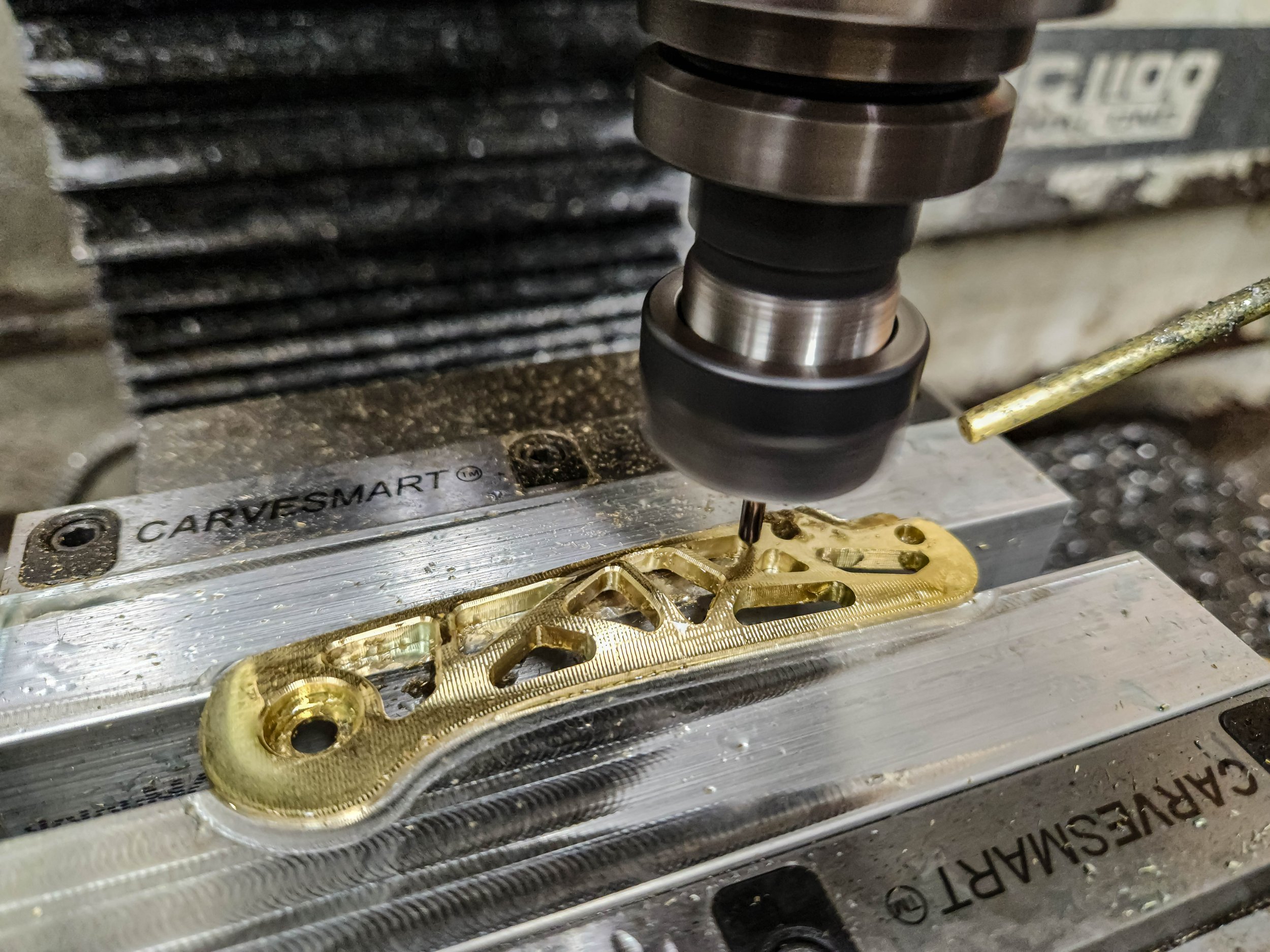
Trying to make smaller holes
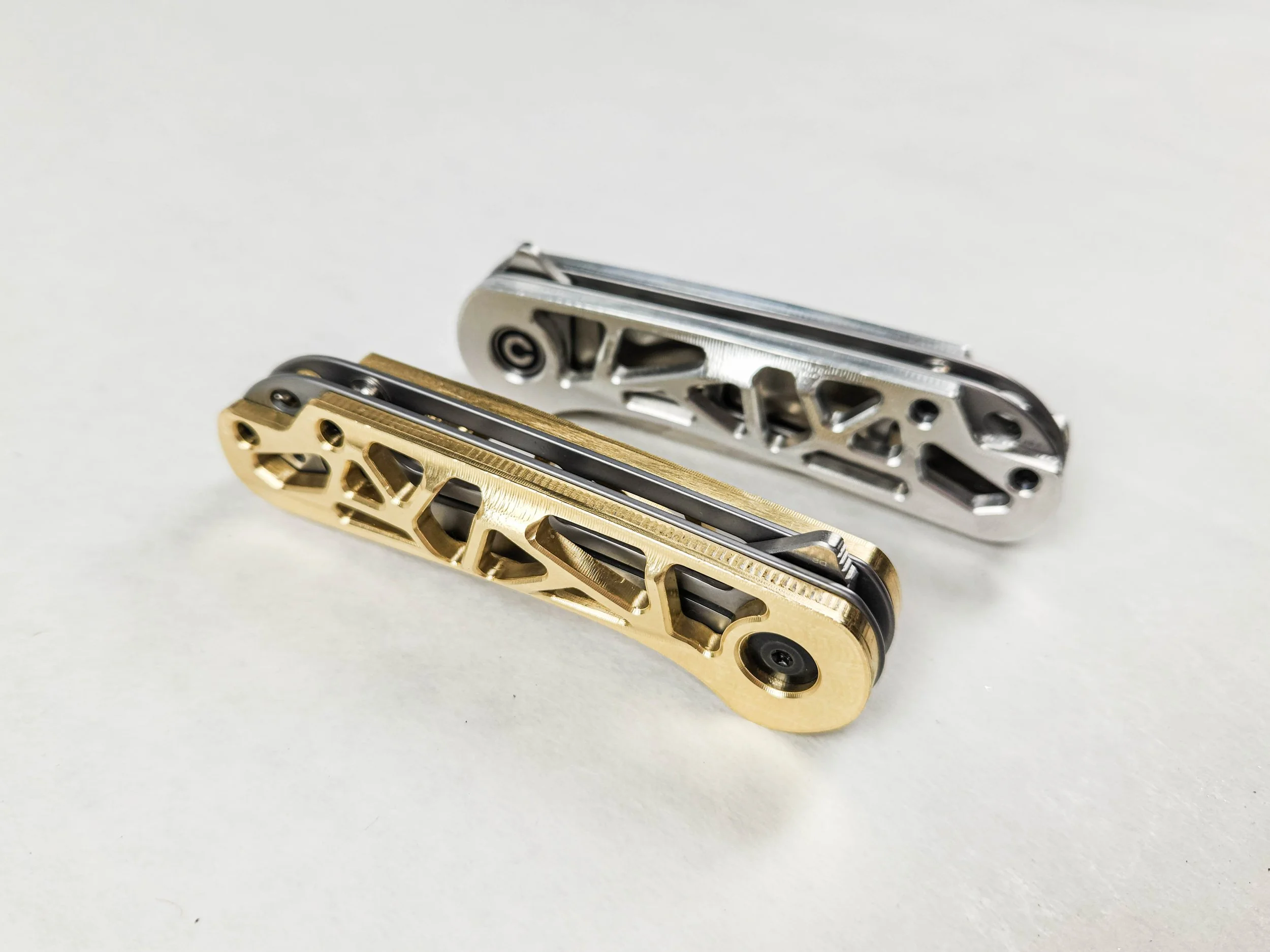
The product
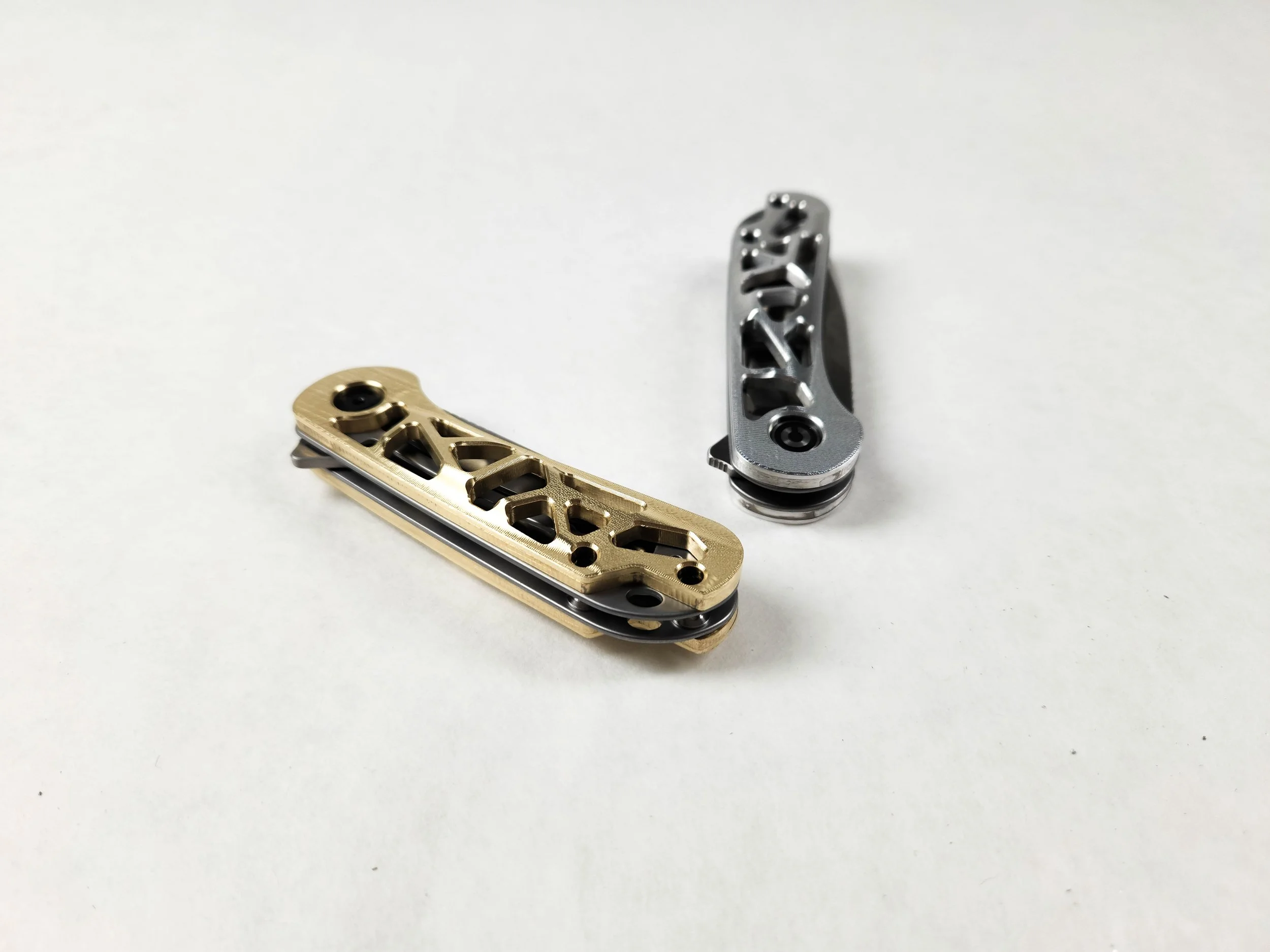
More holes were created
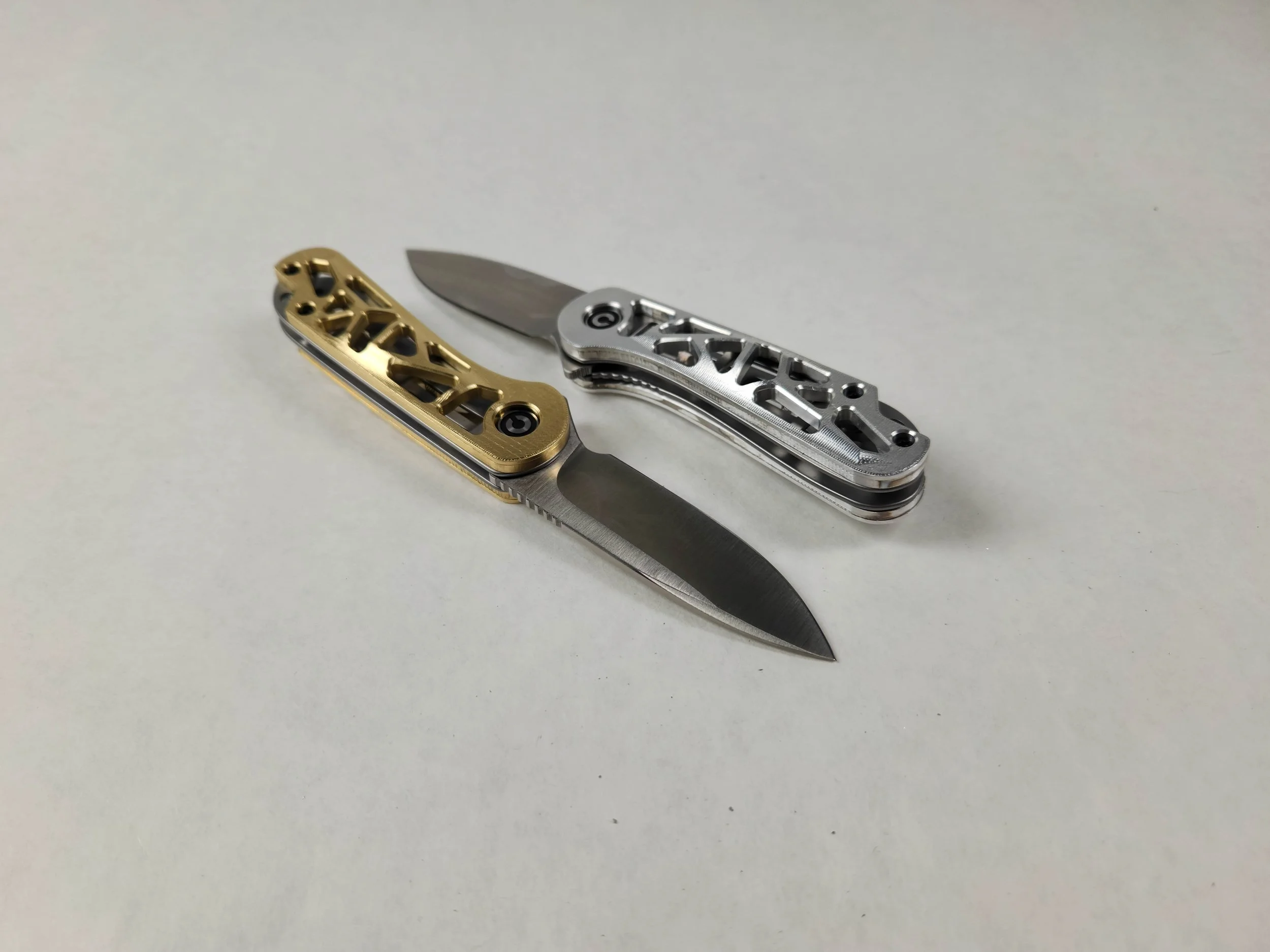
Starting to achieve my vision!
Version 3
Version 3
This was probably the fastest and cleanest milling procedure that I have done so far. Nothing broke and an extreme level of thinness was also achieved to make the lightest version of my design so far as I explored using custom fixture plates instead of using soft jaws. Thinner strands were also introduced to the lattice to make it look more delicate while maintaining most of the strength needed to be a suitable pocketknife.

Using a scanner to check dimensions
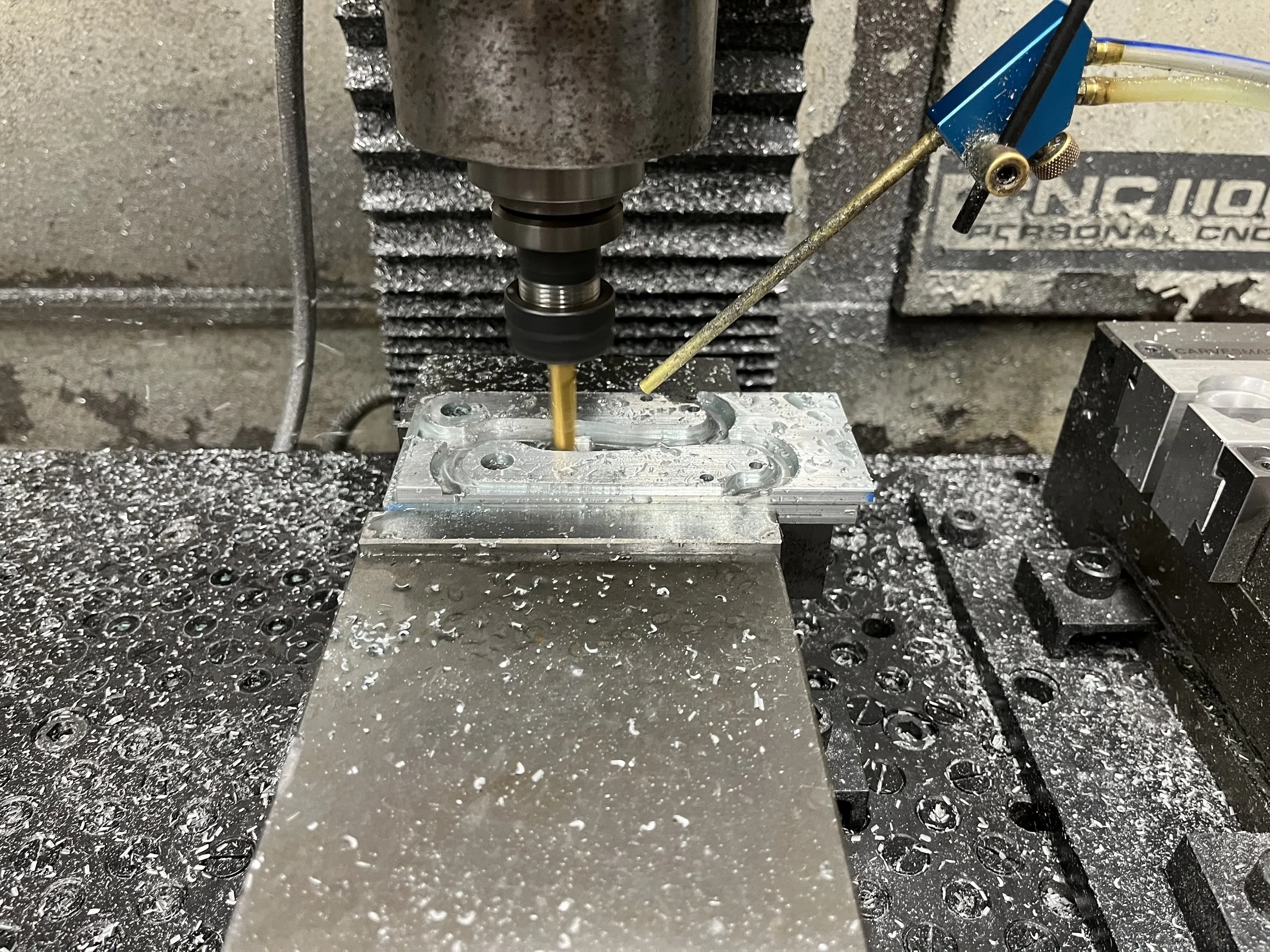
Machining everything all at once
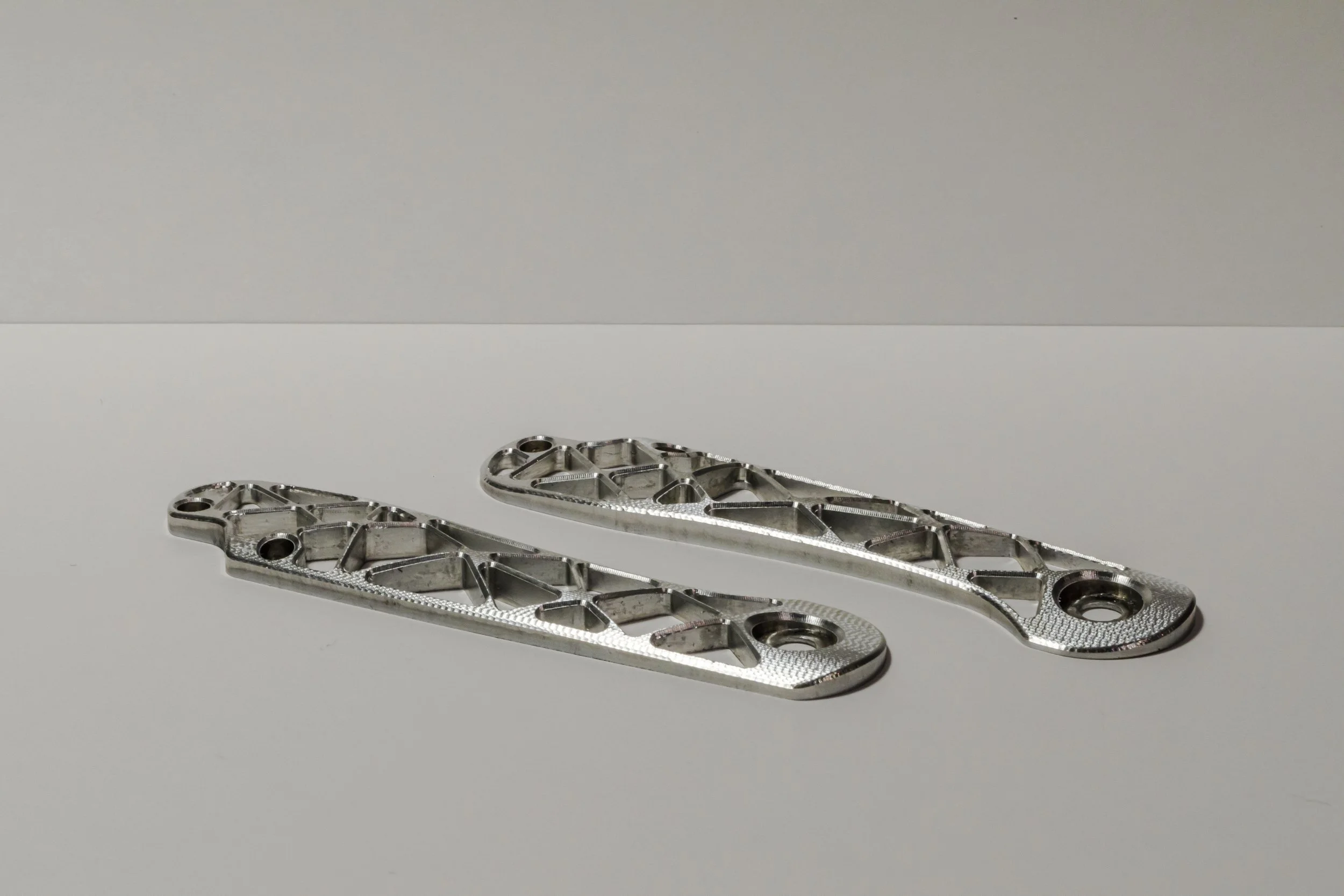
A view of the contour
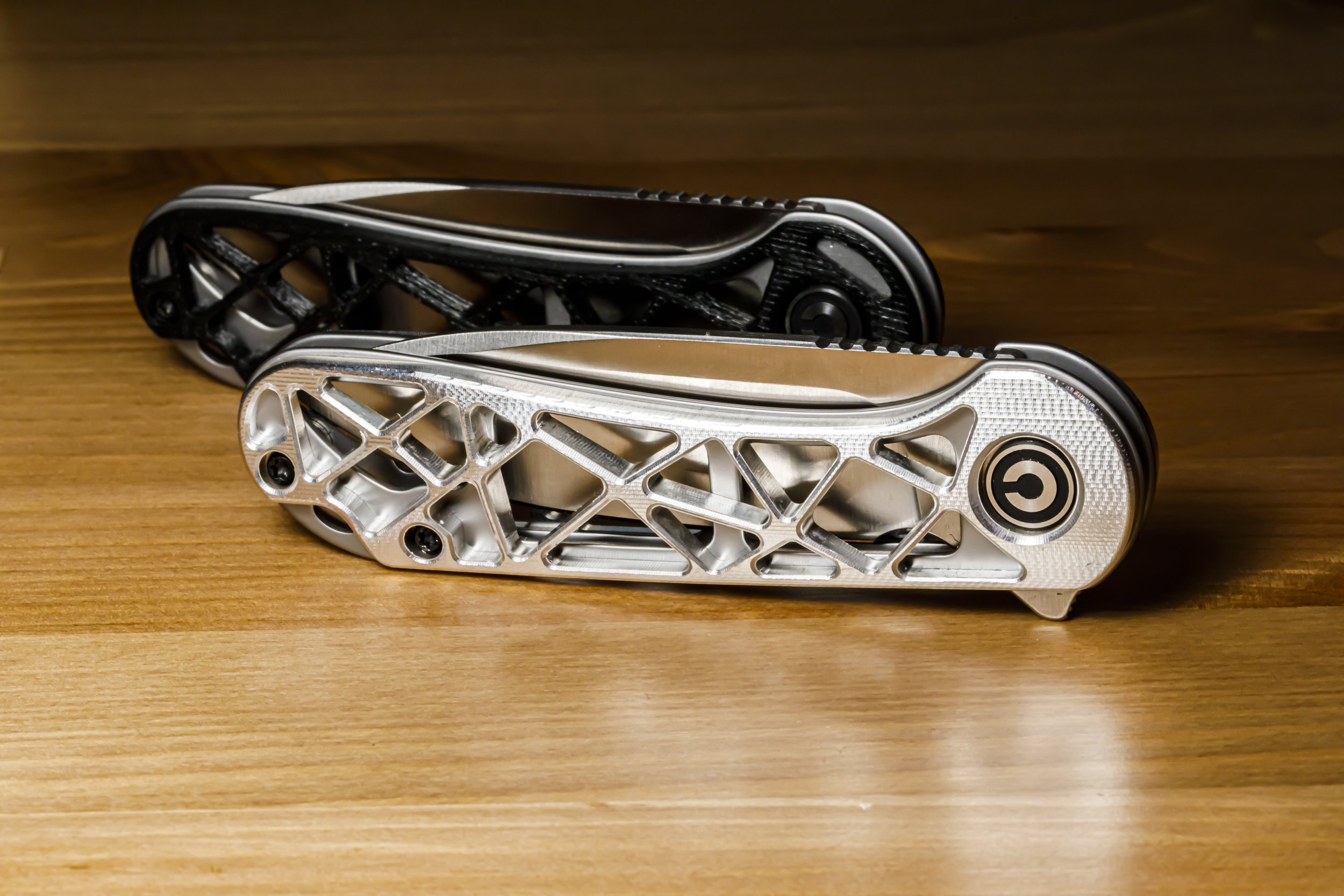
Detailed view of V3
Version 4
Version 4
Feeling confident, I went back to the drawing board with ambitions of making my very own knife instead of just making a modification for something that already exists. CAD was the natural first step as I designed with the people that I interviewed to make something truly unique. This time, I made everything myself, blade and all. The design closely follows the ethos of a traditional Higo no Kami.

Mocking it up in CAD

I found out at this stage that this knife was way too big.
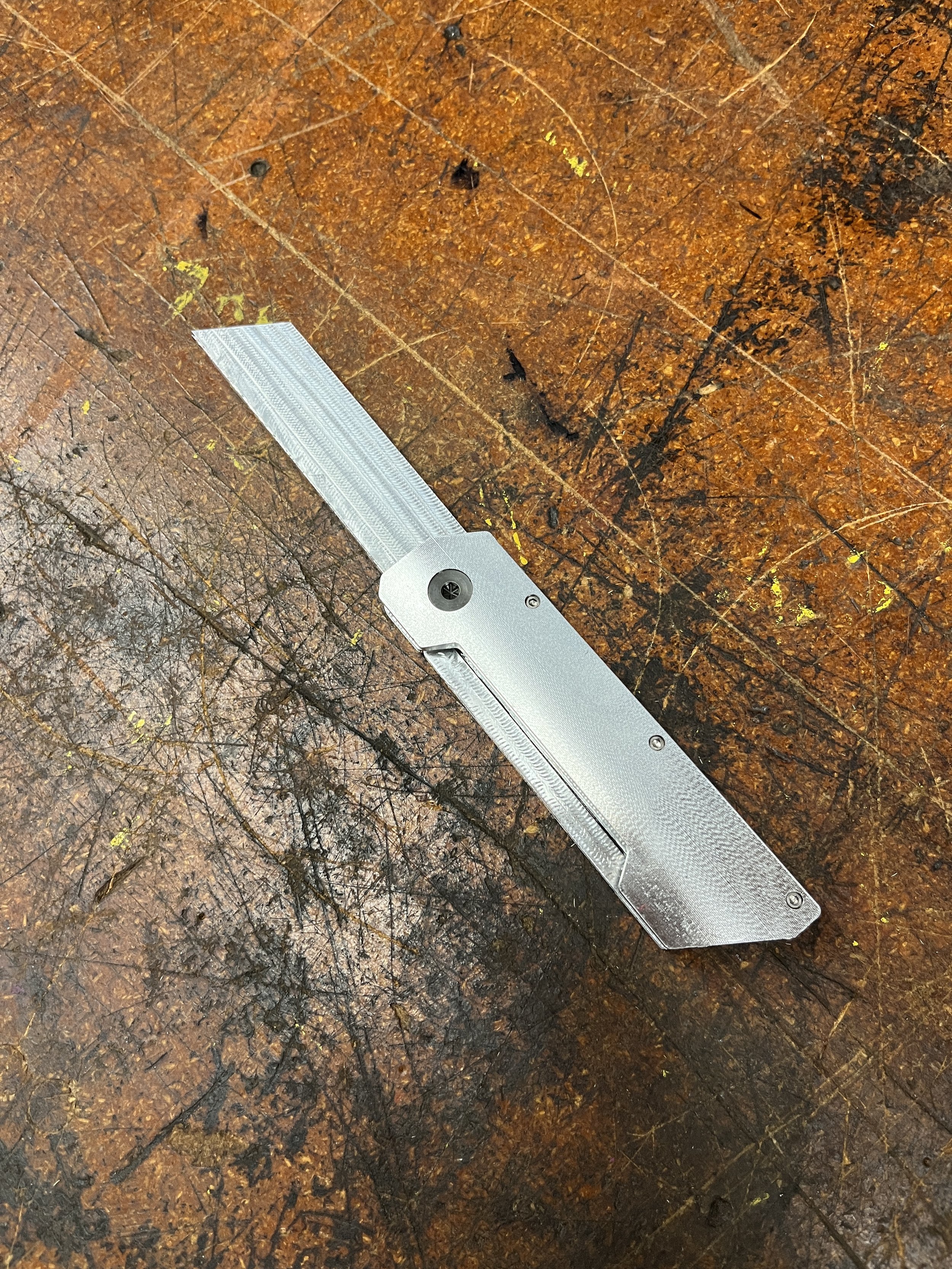
Mockup after edits to structure to make it shorter.
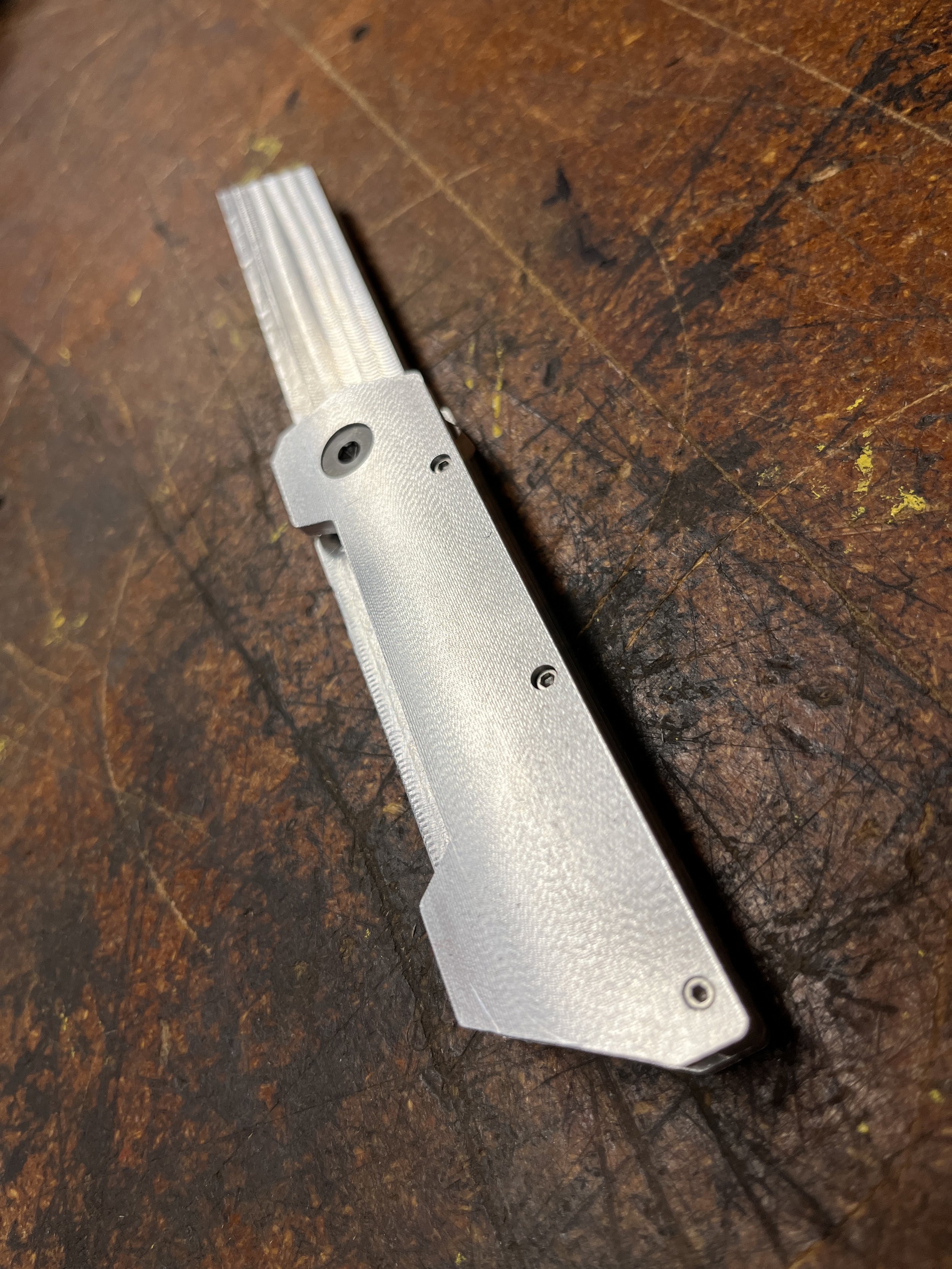
Realizing that a traditional flipper will not work with my design.
Modern Higo MKV
Modern Higo MKV
While designing version 4, I realized that I had much to change in the design to make it the ultimate iteration. This one is going to be perfect and align with the research I have conducted so far. In order to practice mass manufacturing, I am also going to create a fixture plate that will allow me to make multiple knives at once to speed up the production. At the end, I will have 12 fully functional knives amounting to 200hr of machine time.
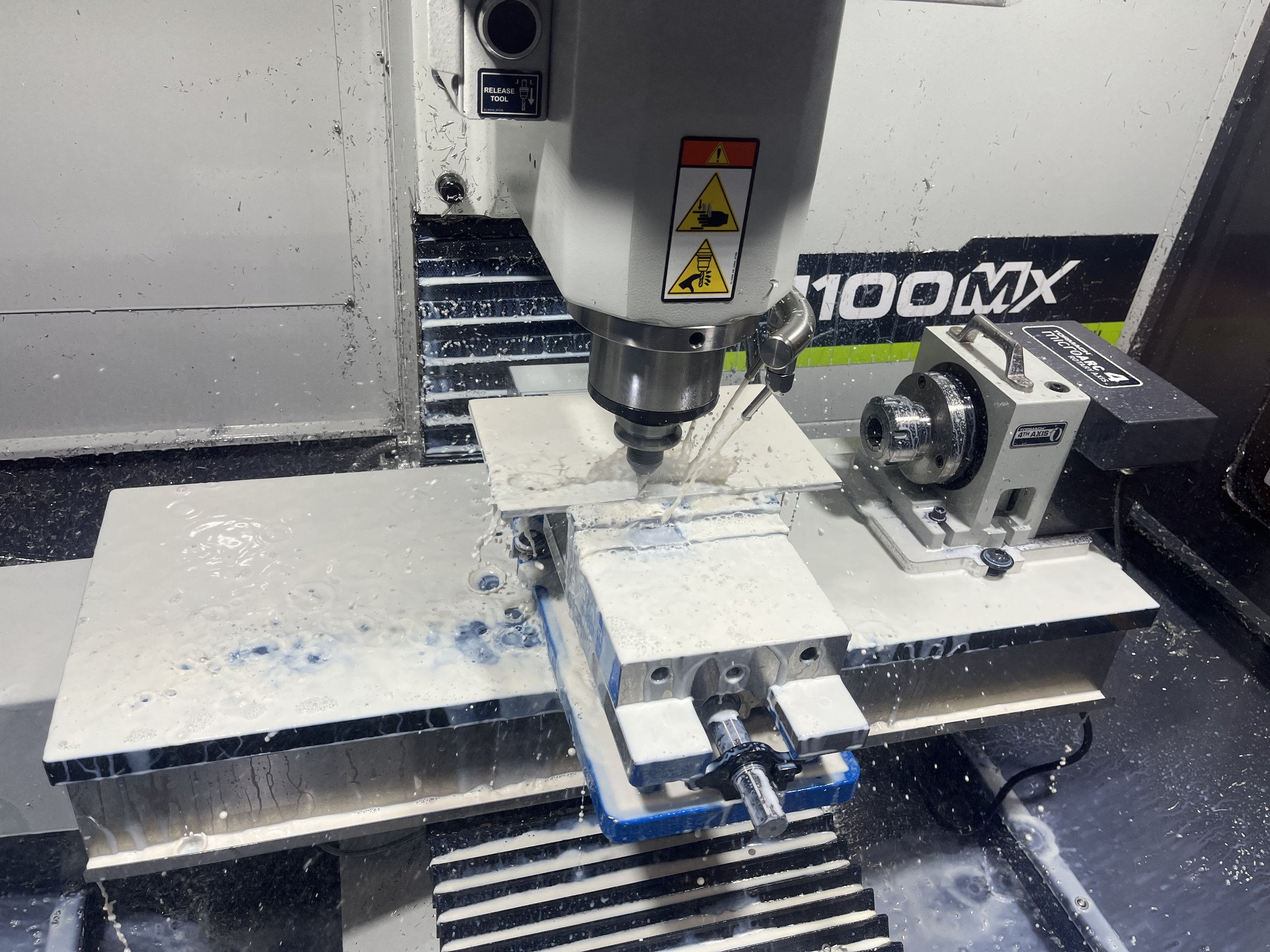
Blanking out the profile
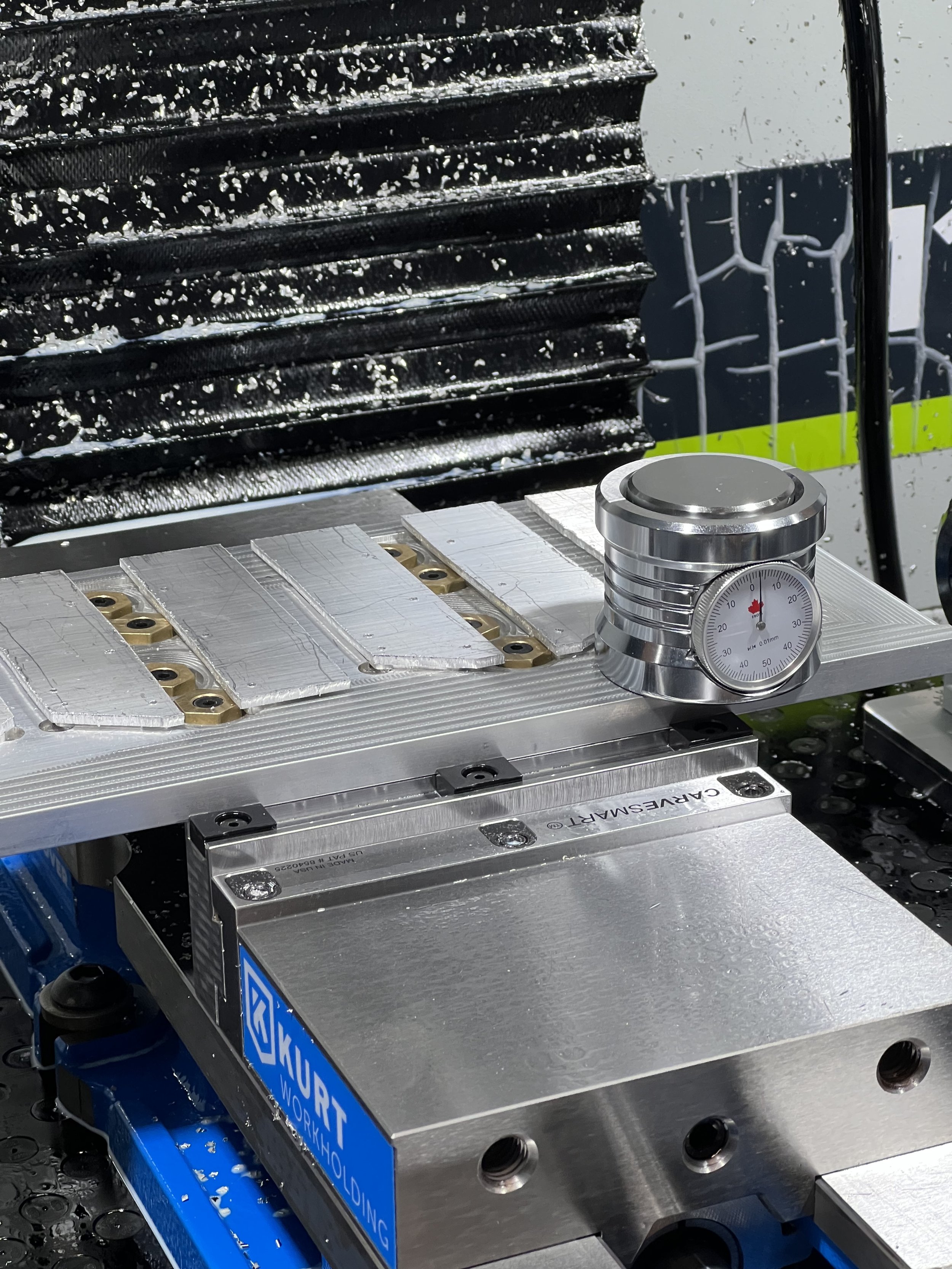
Setting the height of the plate
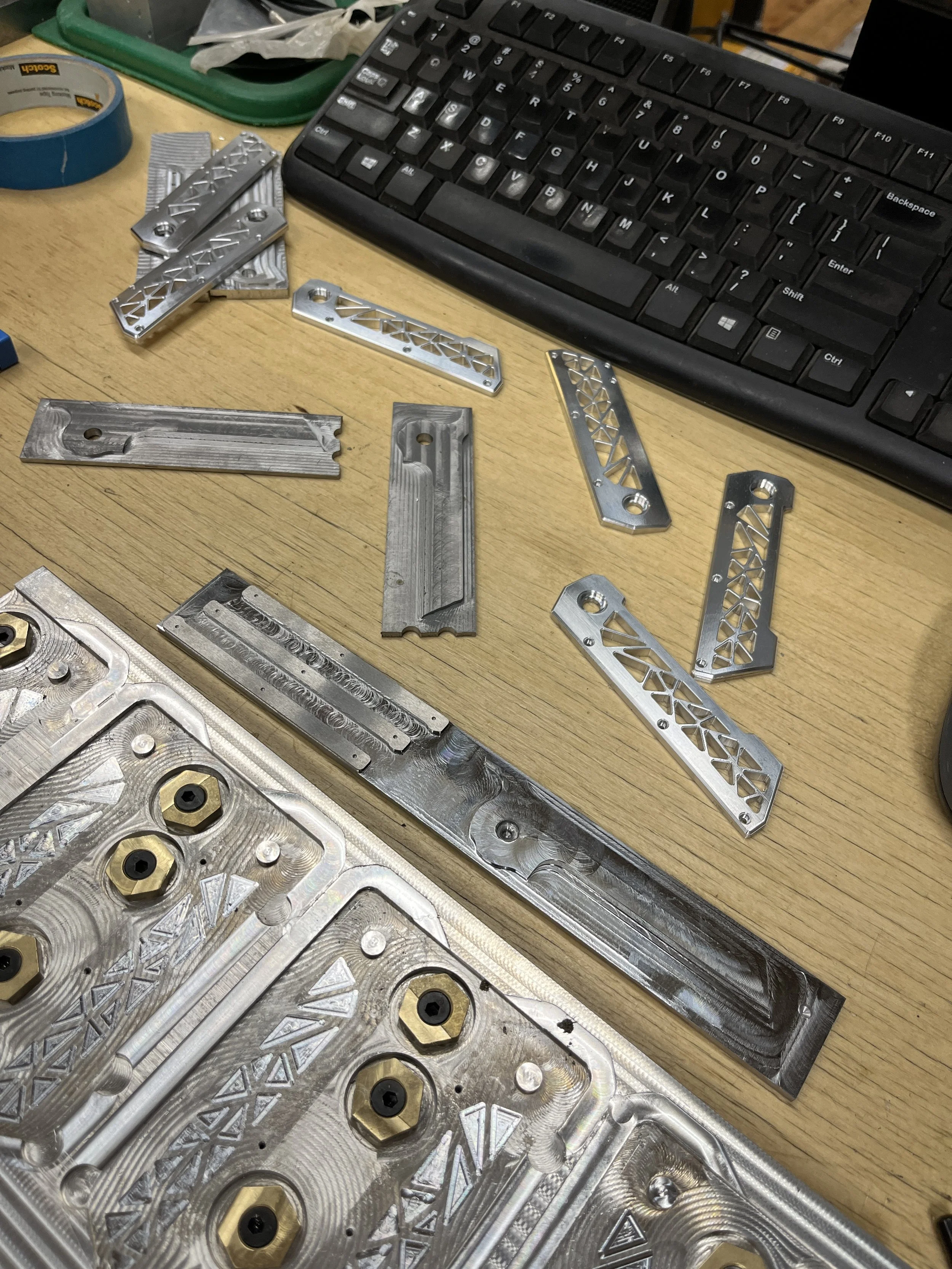
Making the steel components

One completed plate of scales
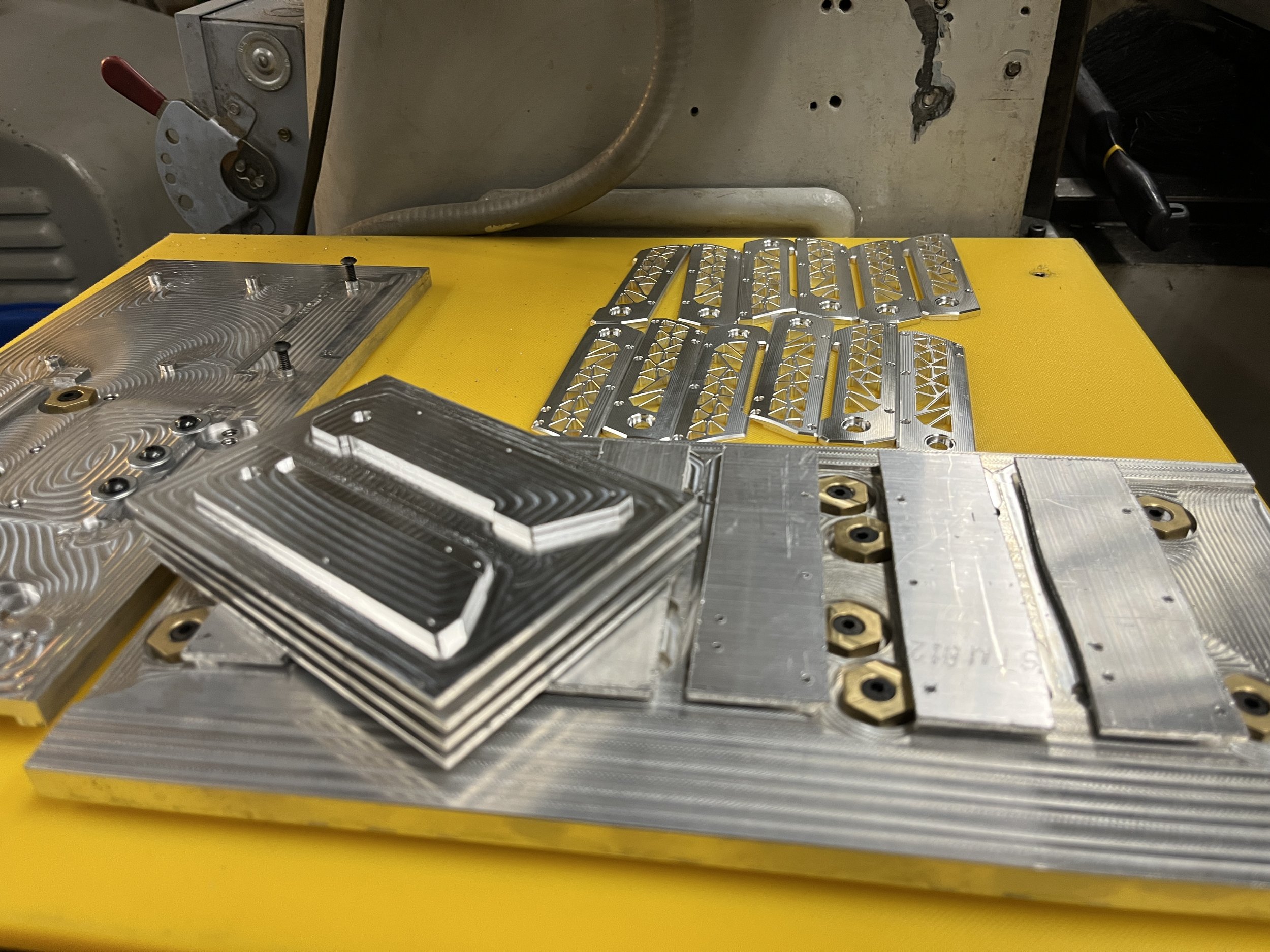
The production line
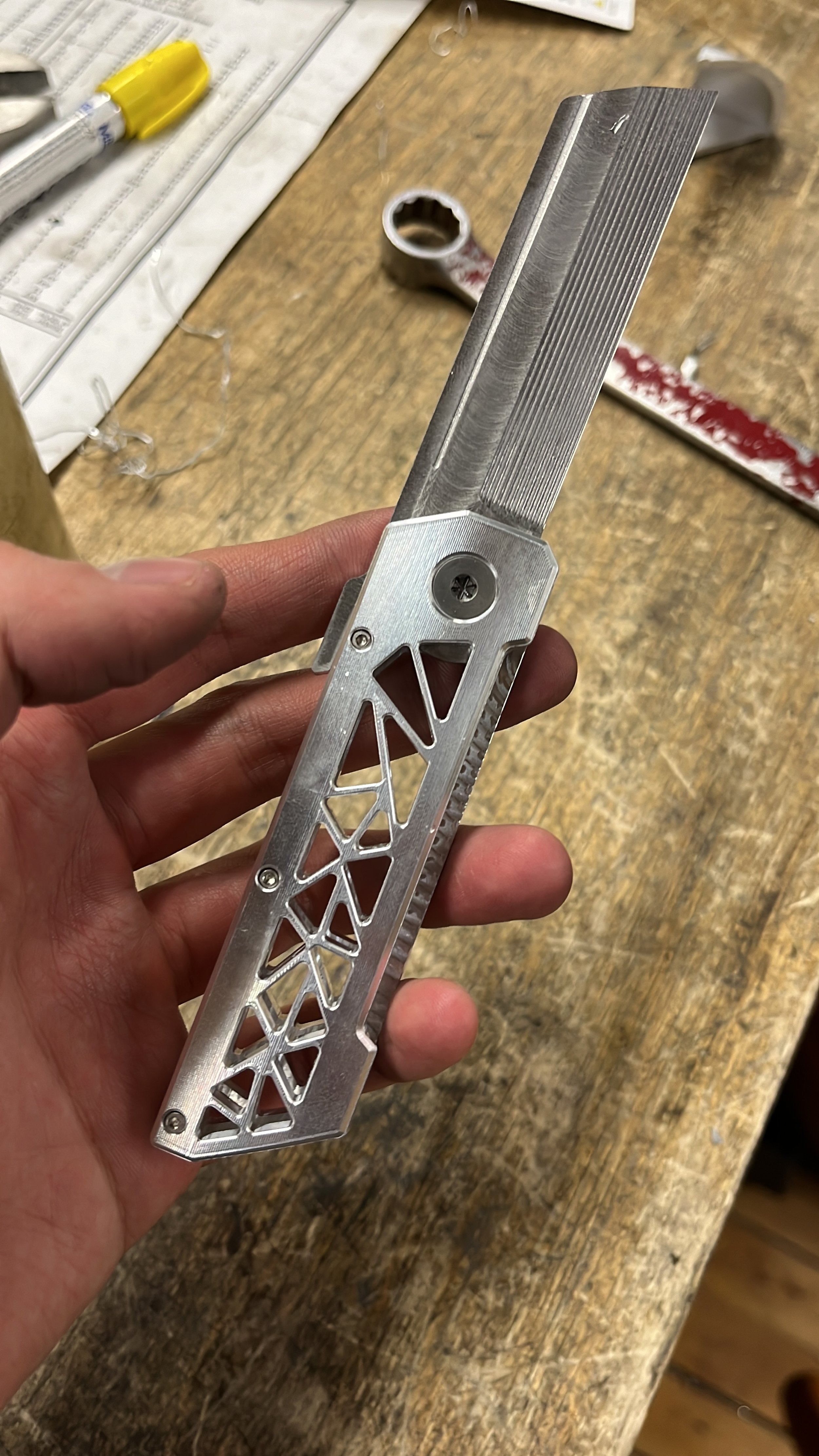
The first test fit

Ready to be hardened at RI Heat Treating Co.
The Final Product
The End of an Era
This project has been an emotional rollercoaster ride. So many people have come out to help me along the way even in the face of a department that has given up on my hopes of pushing the limits of what is possible. There were many times when I wanted to give up and just lay down my tools and cry myself to sleep. However, my friends all came together to help me keep this project going. Alex Wu, who came in the middle of the night just to cheer me on. Will Reeves, who was always there to give me some of his wisdom from his life experiences. Linlin Yu, who was there to tell me to rest up, there will always be tomorrow, and everything will be ok.
I will be leaving one of my knives in trust of the RISD Industrial Design Metal Shop. I hope that this project will serve to inspire the many people that will come after me and show them what is possible here.
The future is limitless, so push the boundaries of what is possible.
“I know you will make this work, one way or another….” - Will Reeves 2023
This Project is on display at the RISD Industrial Design Gallery’s first “The Metal Show” as its centerpiece from March 8th to 22nd of 2024. A show dedicated to the Metal Shop Monitors and Faculty who work with us. Meant to inspire the next group of people who will come and inhabit the shop to make their wildest dreams come true.